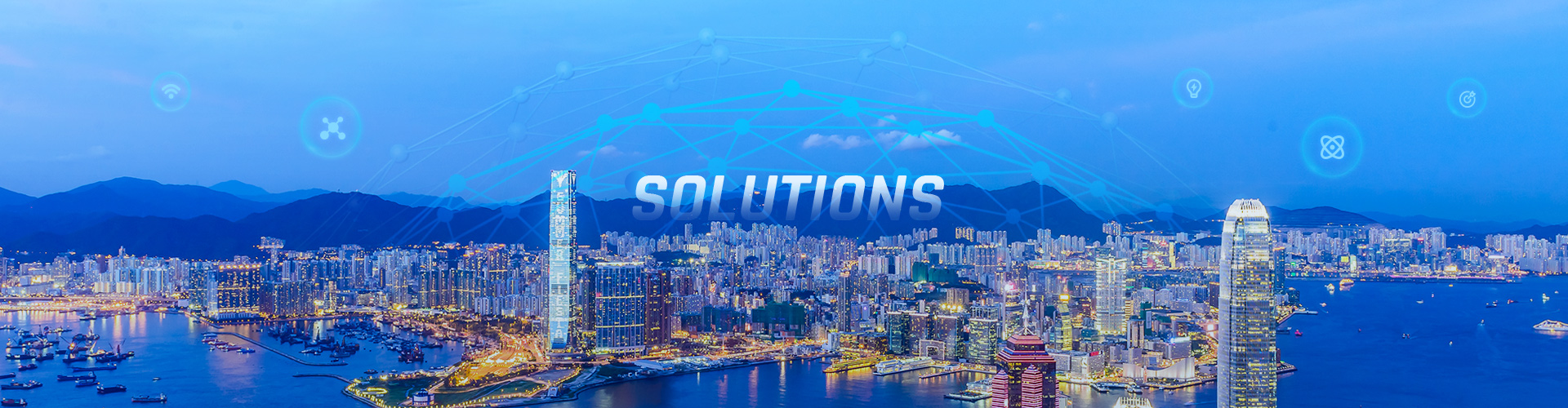
SULOTIONS
How to choose the appropriate barcode scanner for the welding machine
In the harsh welding operation environment, choosing a barcode scanner that combines precise recognition, industrial-grade protection and seamless integration is of vital importance. Modern welding equipment requires scanners that can read barcodes on curved or reflective metal surfaces while resisting dust, water splashes and accidental drops. Industrial-grade barcode scanners are recommended for mobile welding operations and large steel structure workshops, and industrial-grade barcode scanners need to strike a perfect balance between flexibility and industrial protection.
1. Super decoding performance
Data Matrix (DM code) has become the gold standard in the field of welding traceability due to its small size and high fault tolerance. In high-temperature welding scenarios, only the barcode scanner equipped with a high-precision 2D imaging sensor can read the worn DPM code (direct part marking). It is recommended to choose the ISO/IEC 16022 certified equipment, which can recognize laser etching codes tilted at 60°. Industrial-grade scanners adopt red and white hybrid light source technology, which can penetrate the reflective surfaces of welding consumables or metal parts. Equipped with a 1280×800 pixel high-resolution sensor, it can accurately identify various barcodes, including micro DM codes smaller than 0.5mm, even in low-light conditions. YJD190 Industrial DM code scanner, YJD190 Welding waterproof barcode gun, YJD190 anti-drop Bluetooth scanner gun,
2. Real-time Data Transmission Protocol
Give priority to choosing models that support Bluetooth 5.0, Wi-Fi 6E or USB-C industrial interfaces. Equipped with multi-protocol ports (RS-232, Ethernet), it can seamlessly transfer data to the PLC or MES system of the welding machine, ensuring the traceability of mass production. H210 high-speed Data Matrix reading, H210 IP67 industrial scanning equipment, H210 industrial-grade barcode scanner,
3. Military-grade protection design
Select equipment with *IP54/IP67 protection grade * and *MIL-STD-810G military standard certification *, which can withstand the impact of a 1.5-meter drop onto concrete - this is crucial for a busy welding workshop. Anti-fog lenses and anti-corrosion casings further enhance the service life of the equipment in damp or dusty environments. H81L waterproof and shockproof barcode scanner, H81L DM code reading device, H81L welding workshop data collection,
4. Compatibility of welding process flow
Ensure that the scanner is compatible with ERP systems (such as SAP, Oracle) and welding-specific software. Models that support the SDK development package can customize the tracking of electrode batches, welding parameters or quality inspection data. YJD190 highly durable scanning terminal, YJD190 industrial wireless barcode scanner, YJD190 welding MES system integration, YJD190 real-time data collection terminal,
5. Forward-looking technologies in AI and IoT
The new generation of scanners is equipped with built-in AI auto-focusing and fault warning functions, reducing downtime. By connecting with the platform, real-time analysis of welding quality data can be achieved. Supporting cloud traceability, the scanner can automatically upload batch data of welding materials to the cloud dashboard, facilitating real-time monitoring of compliance by global quality inspection teams. H210 high-strength DM scanner, H210 anti-electromagnetic interference scanning device, H210 explosion-proof barcode scanner,
6. Summarize the core selection criteria
High-temperature resistance and explosion-proof performance: Select models with an operating temperature range of -30°C to 50°C, suitable for foundry workshops or outdoor welding scenarios. For welding in hazardous areas, such as when reading the DM code of gas cylinders or pressure vessels, the risk of explosion and combustion must be eliminated.
Anti-strong light technology: Welding arcs can produce high-intensity glare. The scanner equipped with a polarizing filter and adaptive exposure adjustment can maintain precise recognition in the presence of ultraviolet interference.
Seamless integration of ERP system: Select devices that support OPC UA or MQTT protocols, synchronize with the data logs of the welding machine, and meet the requirements of ISO 3834 certification.
Protection requirements: Common metal spatter and oil stains in welding workshops, immersion in 1 meter of water depth, resistance to 2 meters of concrete drop. To perform outstandingly in such extreme environments, our industrial-grade barcode scanners must have the functions of water resistance, dust resistance, drop resistance and oil stain resistance. Through 1D/2D hybrid imaging technology and an IP65 protective housing, barcodes can still be stably read on the curved surface of galvanized steel plates with oil stains. H81L DPM code dedicated reading device, H81L arc Weld compatible barcode scanners
CONTACT US
CONTACT US
CONTACT US

are completed before submitting your inquiry.

We will respond within 24 hours.